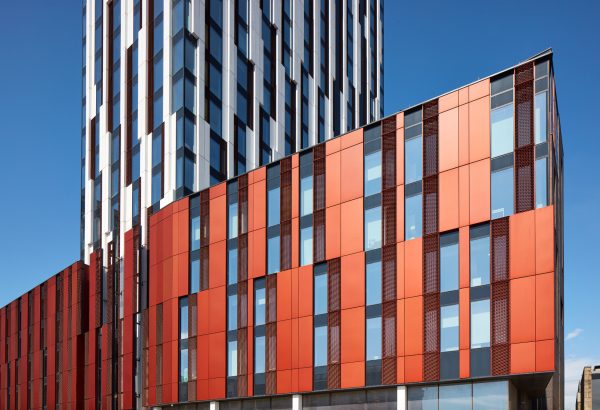
The rise of unitised cladding systems
In recent years, there has been a marked rise in the adoption of modern methods of construction (MMC). We’ve worked on our share of projects over the years that have used a whole system build or volumetric approach, as well as a prefabricated concrete sandwich panel system.
While these methods offer distinct benefits, we’ve often seen that the push for zero carbon has led a shift away from MMC that results in rigid internal layouts towards methods that prioritise adaptability and longevity in layout design.
Consequently, we have noticed piqued interest in unitised cladding systems that integrate the benefits of MMC into developments while continuing to allow for flexible, unrestricted internal layouts.
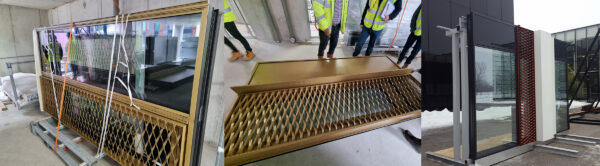
The system involves the assembly of prefabricated units off-site, which are then transported to construction sites for immediate installation. These units usually span one to three modular panels in width and encompass one or two storeys. The panels arrive fully glazed and sealed, complete with gaskets and glazing beads, all meticulously built off-site with high emphasis on quality control and precision.
Now commonly used in tall buildings, the quality control benefits of off-site manufacturing combined with the speed of erection on-site have propelled MMC into serious consideration for smaller-scale projects as well. This shift highlights the versatility and efficacy of MMC across a spectrum of project sizes, promising enhanced efficiency and quality regardless of scale.
Below are some of the benefits of unitised cladding systems.
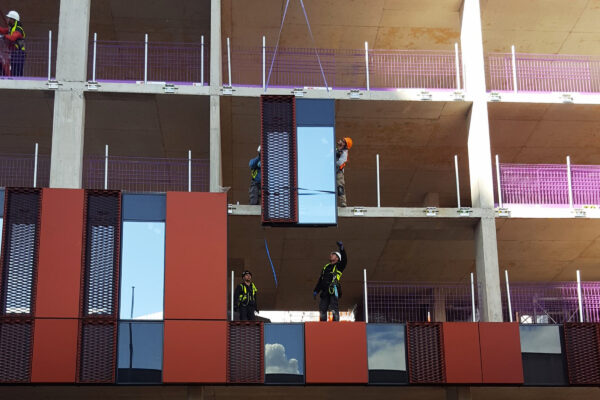
-
Quality control
Unitised panels are manufactured in a controlled environment, ensuring consistent quality. This precision minimises errors and time wasted on site, rectifying issues which may emerge with a more traditional system.
-
Speed of installation
Pre-installing bracketry onto the (typically) concrete frame before unit arrival results in a swift installation, leading to a significant reduction in external envelope construction, time on-site and freeing up time for internal works to progress.
-
Site efficiency
The system is installed from within, eliminating the need for costly scaffolding and mast climbers and improving the health and safety implications of working at height. Deliveries on a just-in-time basis reduce on-site storage requirements, streamlining logistics and maximising workspace efficiency. This lean approach to materials management ensures that resources are utilised effectively and waste is minimised.
-
Detailed design up-front
Due to the prefabricated nature of the system, the design is resolved and coordinated before it arrives on site. While this proactive approach is always desirable, the necessity for precise design-to-build is emphasised with unitised façades, significantly reducing the need for on-site problem-solving and coordination during construction.
-
A single package of works
Finally, consolidating the majority of the external envelope within a single construction package cannot be underestimated. This approach leads to streamlined coordination and a simplified interface between various building components, reducing the risk of errors, conflicts, and delays during construction.
-
Enhanced value
Whilst unitised curtain walling (UCW) systems are generally more costly upfront, the benefits listed above result in a number of efficiencies during the construction process, resulting in a system which provides excellent value.
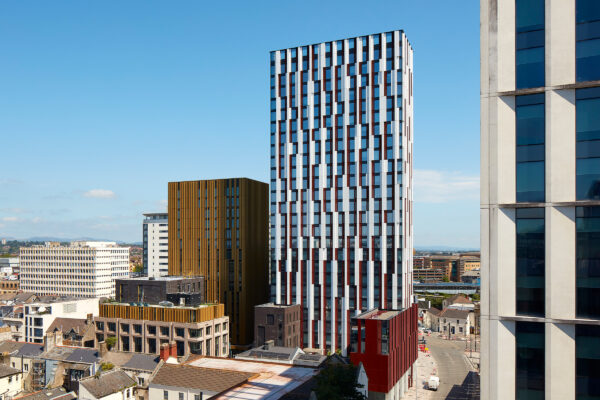
Two of our completed projects in Cardiff utilise unitised cladding. Bridge Street Exchange, a 27-storey student accommodation project completed in 2018 for Watkin Jones Group, is located adjacent to the more recent Verse, a 152-unit build-to-rent (BTR) development for Crossmark.
Our design team’s comprehensive understanding of the system’s intricacies gave both client and contractor confidence in the success of these projects with the assurances that potential risks and issues had been thoroughly considered and addressed.
The buildings were designed with modularity and simplicity in mind, minimising the need for any bespoke or non-standard panels. By incorporating off-site solutions, we estimated an overall reduction in the programme for Bridge Street Exchange by five months.
Central Quay, Cardiff
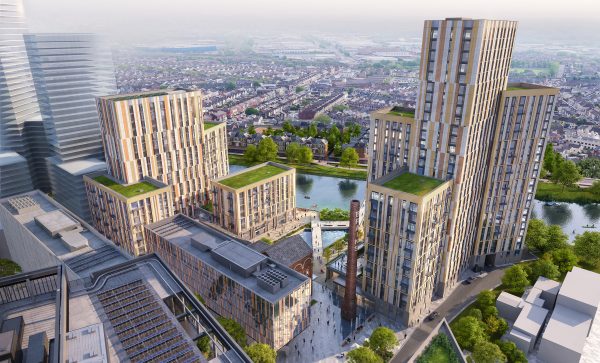
Additionally, the Central Quay BTR development, which is under construction, also employs a unitised construction system. The scale of this development, coupled with the repetitive nature of panels, makes it an ideal candidate for modularisation.
Bridgend College Town Centre Campus
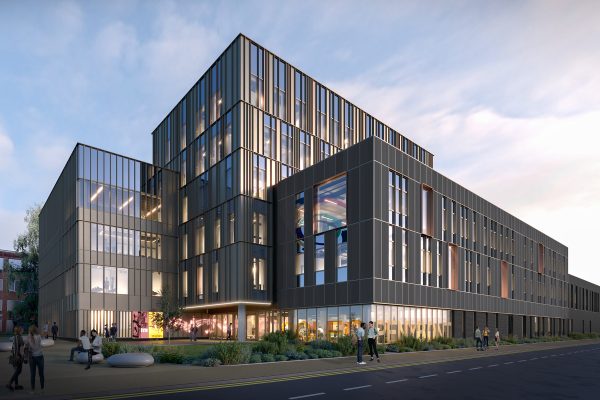
Furthermore, construction has started on Bridgend College’s Town Centre Campus. Despite being a lower-scale building in terms of height, this building comprises 13,000m2 of educational and community facilities. This is an example of where we’re starting to see the benefits of UCW systems being recognised in alternative building typologies. In this case, the building envelope will be designed to Passivhaus standards, achieving exceptional thermal performance and airtightness.
Unitised cladding emerges as a versatile solution, integrating good design, efficiency, and safety across various building typologies. Whilst initial capital outlay can be more than alternative façade systems, the benefits are significant, and the industry is starting to take this system seriously as a realistic method for building façade systems on medium scale as well as tall buildings.
If you’re interested in exploring how modern methods of construction can provide efficiencies in your project, please get in touch.
studio@rioarchitects.com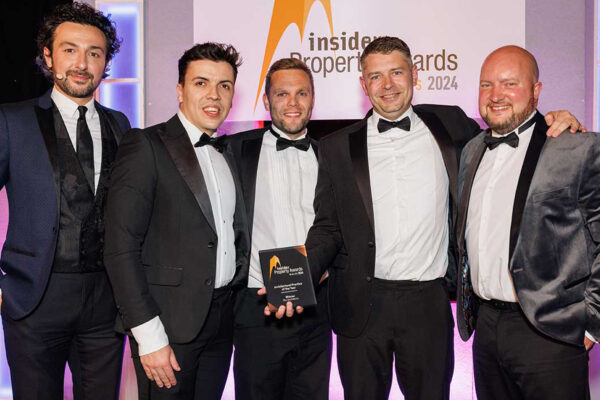