
Delivering successful MMC solutions
There are many reasons why a building’s construction methodology may need to change during a project – whether a result of unforeseen technical difficulties, budget constraints or contractor preference. One such project where this was the case was our recently completed Live Oasis St Albans Place project in Leeds.
Live Oasis St Albans Place is the latest and largest of YPP’s student accommodation schemes to date – a flagship scheme which builds on its reputation for high-quality student accommodation with luxurious interiors and cutting-edge contemporary building design.
The project involved a particularly challenging site in the heart of Leeds, a tight site footprint bounded by busy roads and adjacent to a fully occupied student accommodation.
The building was originally designed as an in situ concrete frame with an external envelope, and a combination of GRC and aluminium rainscreen cladding.
Ambitious from the start, the construction programme was just 24 months from mobilisation to completion, with students needing to move in September 2023 – there was no room for delays.
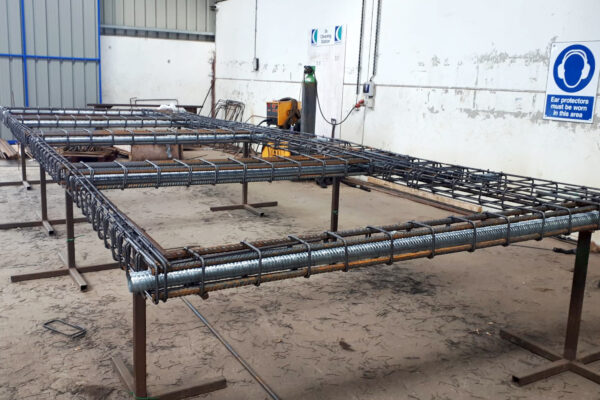
A new build methodology
A new constructional methodology was adopted for the build, using Creagh’s Rapidres system – a form of MMC using precast flat panels. The external envelope comprises load-bearing prefabricated precast concrete sandwich panels (with windows and mesh screens pre-installed), precast concrete wall panels forming the core and cross walls and hollow core concrete planks forming the floors.
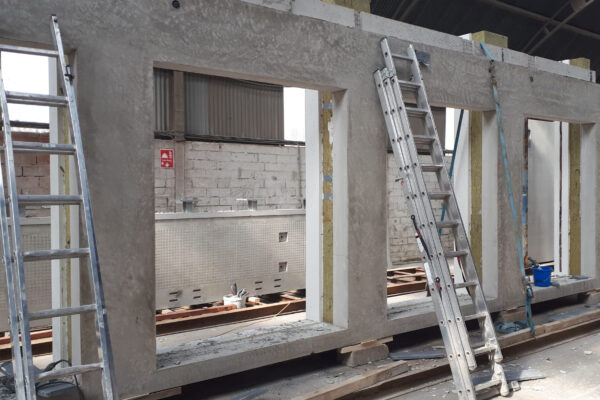
The Rapidres system has the advantage of allowing components to be pre-installed in factory conditions – including the installation of insulation, electrical conduit, doors/windows, and guarding – allowing for an accelerated build on site.
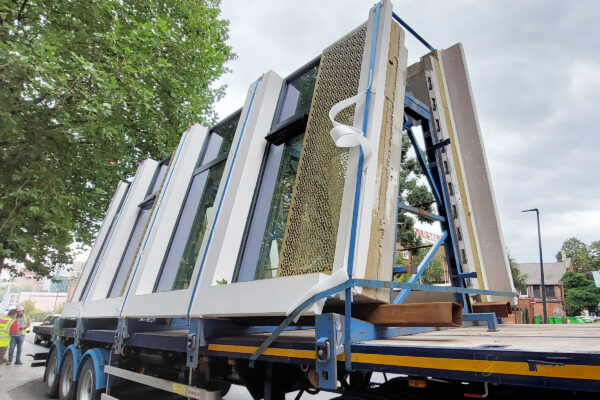
Rapid design coordination
When using MMC, early engagement is typically required to ensure the building design aligns with the construction methodology and is developed to suit the system’s particular parameters.
It also allows coordination between the structural elements, spatial layouts and services.
Traditional methods of construction generally allow design adjustments to be made up to the point that components are built on-site (and even during their construction). However, prefabricated systems, such as Rapidres, require decisions to be made much earlier in the process, with time needed for the manufacturer and delivery of panels to site. It includes the MEP design, which must be signed off early to allow cast-in conduit and socket locations to be set out in the correct locations. The composite nature of the panels also limits the ability to make changes later, placing pressure on design teams to get those decisions right the first time.
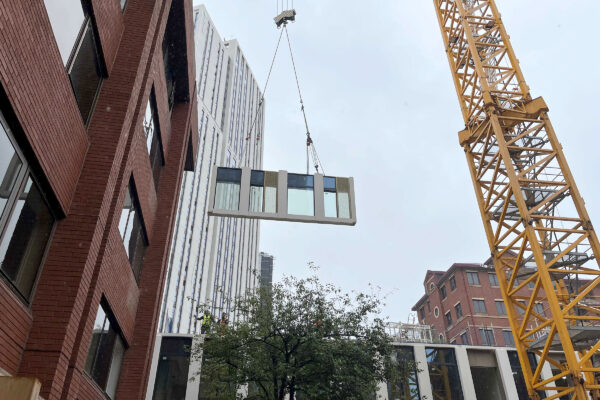
On this project, the decision to switch to the Rapidres prefabricated system occurred after technical design had commenced. The switch in construction methodology required substantial redesign, including changes to external finishes, window reveals, window proportions and pillar sizes. As a result, careful planning and re-evaluation of fire and acoustic strategies became necessary.
The team successfully completed the re-design process despite facing several challenges. This accomplishment was made possible through close collaboration and an intense period of design development to expedite design decisions. The project team met the challenge and achieved their goal through a concerted effort and ‘can-do’ attitude.
Every project and every site brings unique challenges. Live Oasis St Albans Place was an opportunity to realise value, and we advocate early engagement with the system manufacturer to streamline the design process and prevent abortive work.
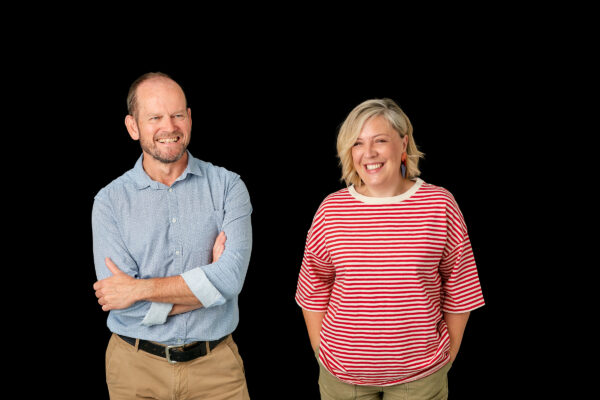